HISTORY OF DENSO SPARK PLUG
HISTORY OF
DENSO SPARK PLUG
●
1959
P2 plug
1962
P3 plug
1970
Wide plug
1972
G plug
1973
Resistor plug
HISTORY
1959 – 1974
Technology Development – Issues
1955, concluded technical assistance agreement with Robert Bosch.
1957, instituted the spark plug lab and started the introduction of plug technology from Bosch.
Dispatched engineers to each other starting in 1958 with the aim of quickly learning the manufacturing technology.
Implemented improvement activities and creative efforts and launched the sales of the P2 plug with excellent mass producibility a year later in 1959. The speed of development was fairly high considering that we started from a base of zero.
In 1960, we were awarded an order for plugs from Toyota Motor Corporation (at that time).
The P2 plug was adopted for the Type R engine installed in the Crown and other cars.
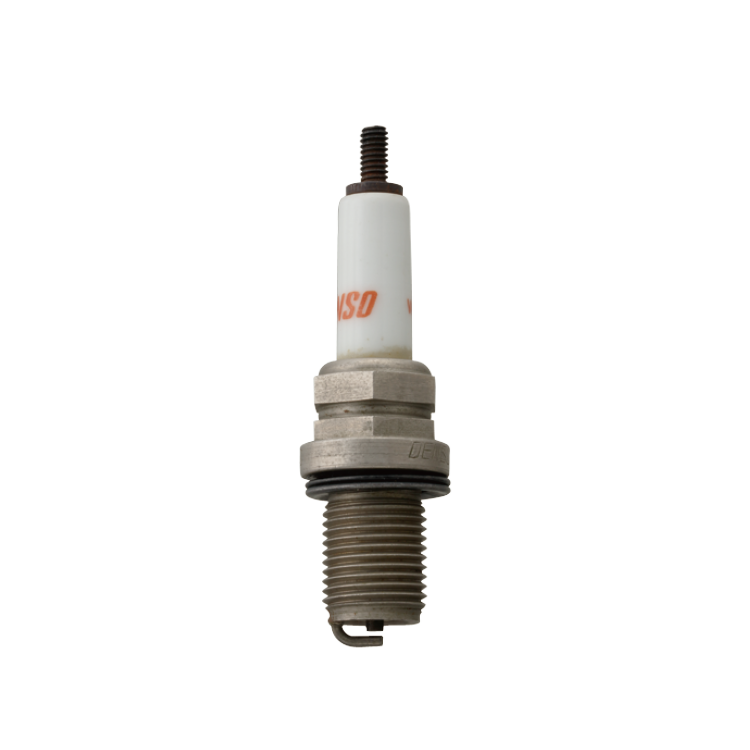
P2 plug
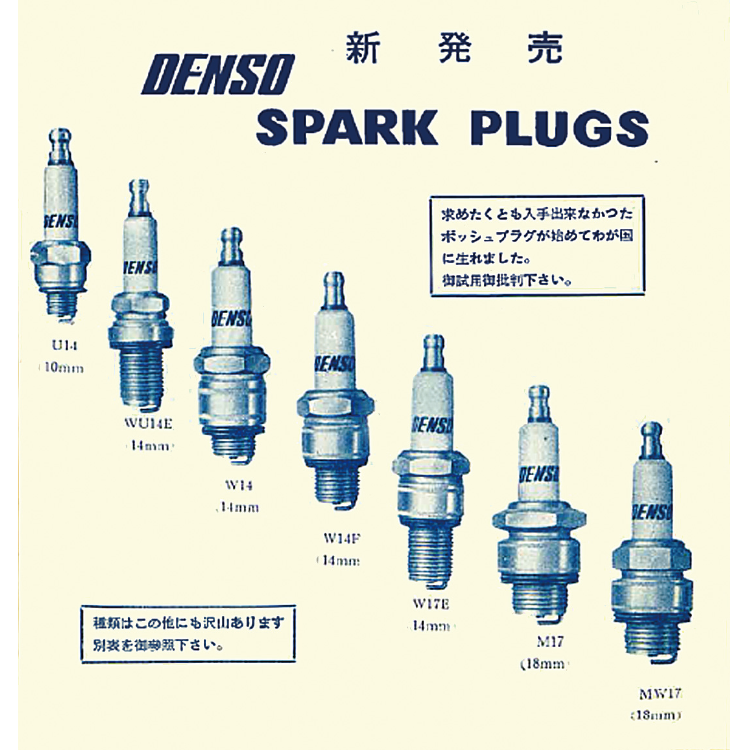
“P2” Plug announcement reception
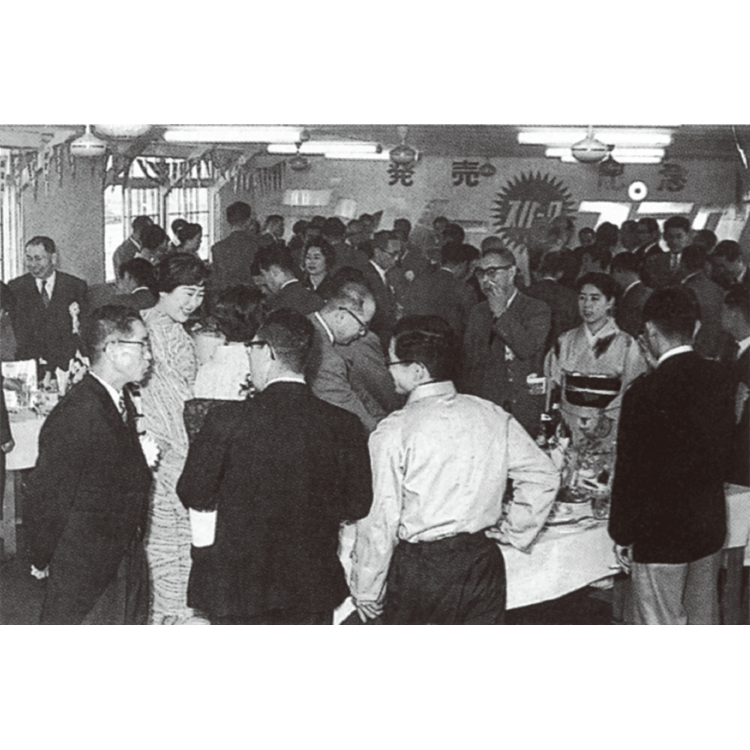
“P2” Plug announcement reception
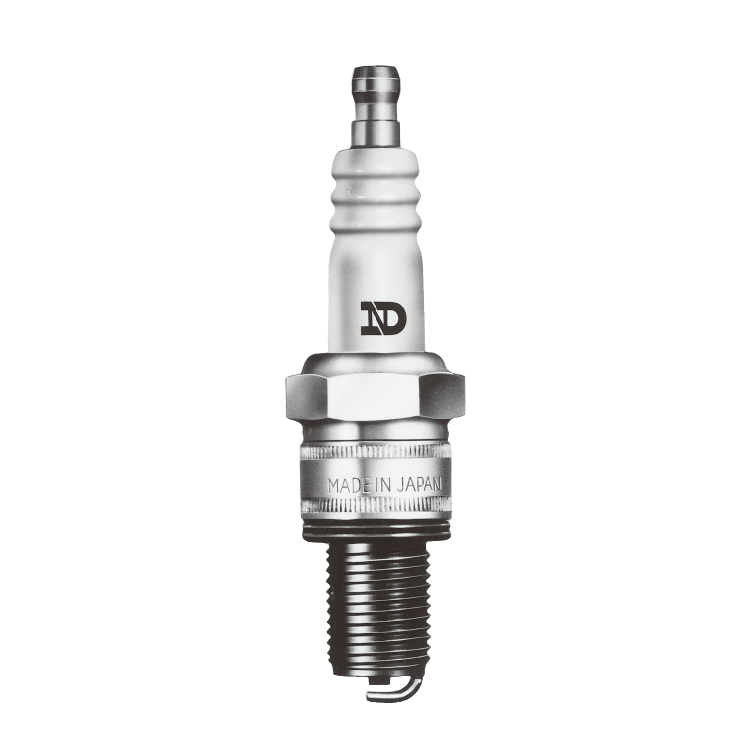
P3 plug
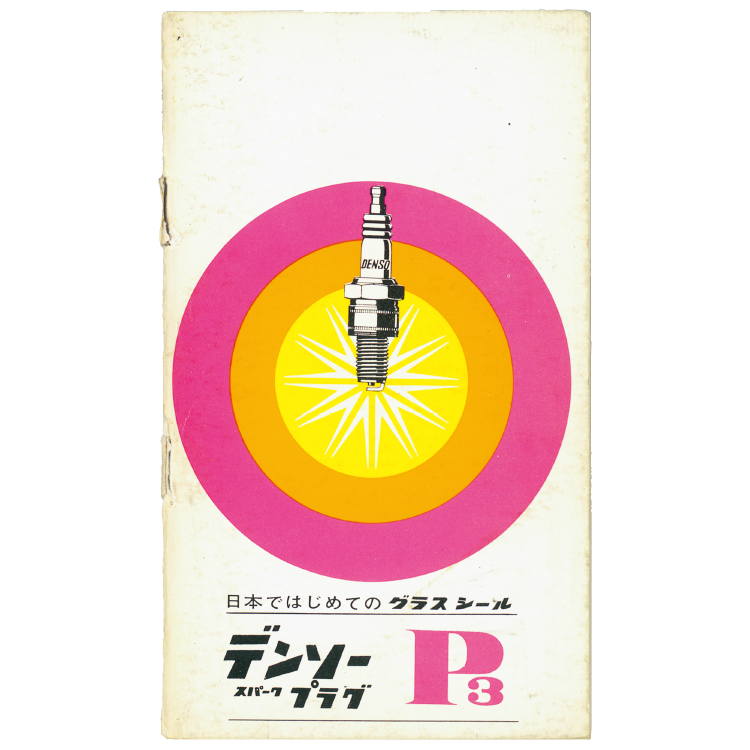
“P3 plug” pamphlet
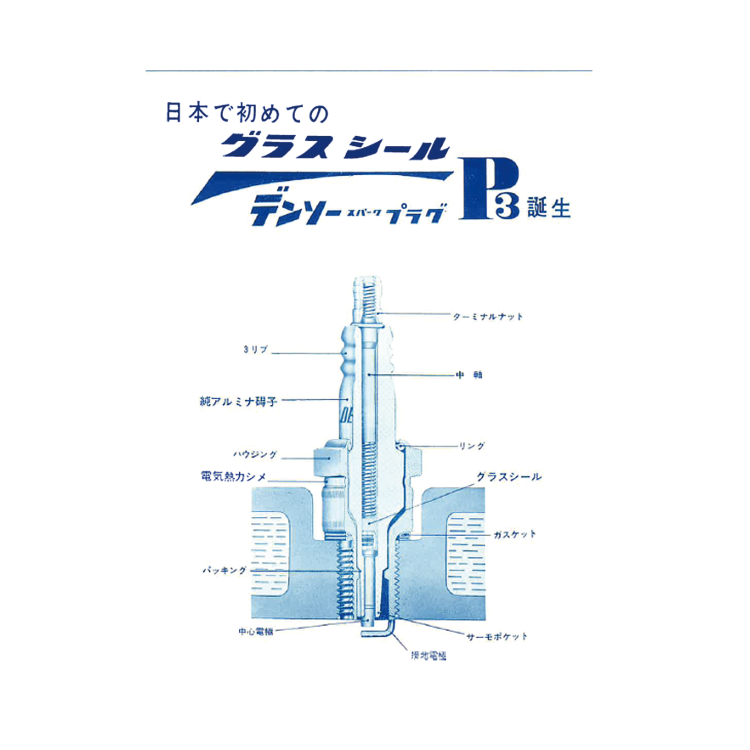
“DENSO Technical Report” Sep 1962 Volume
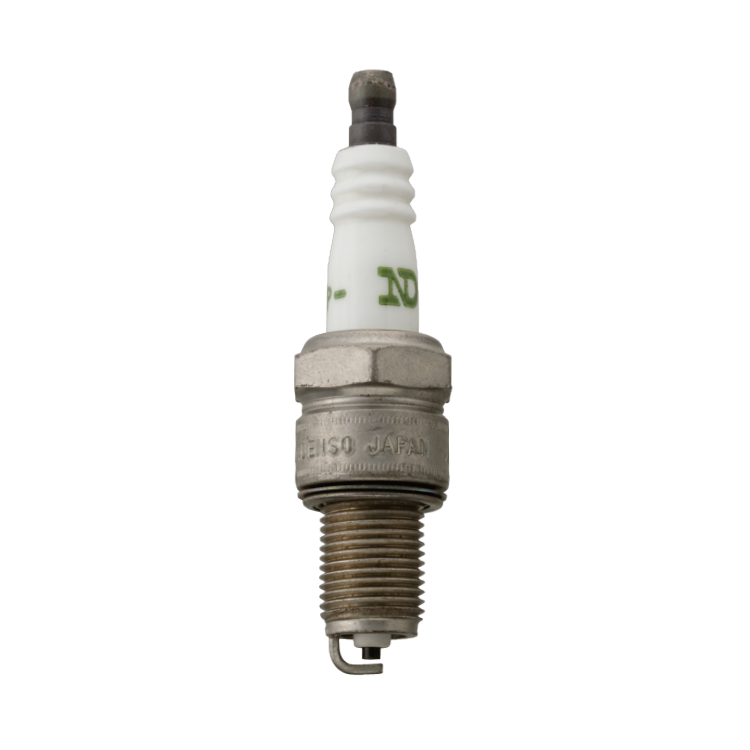
Wide plug
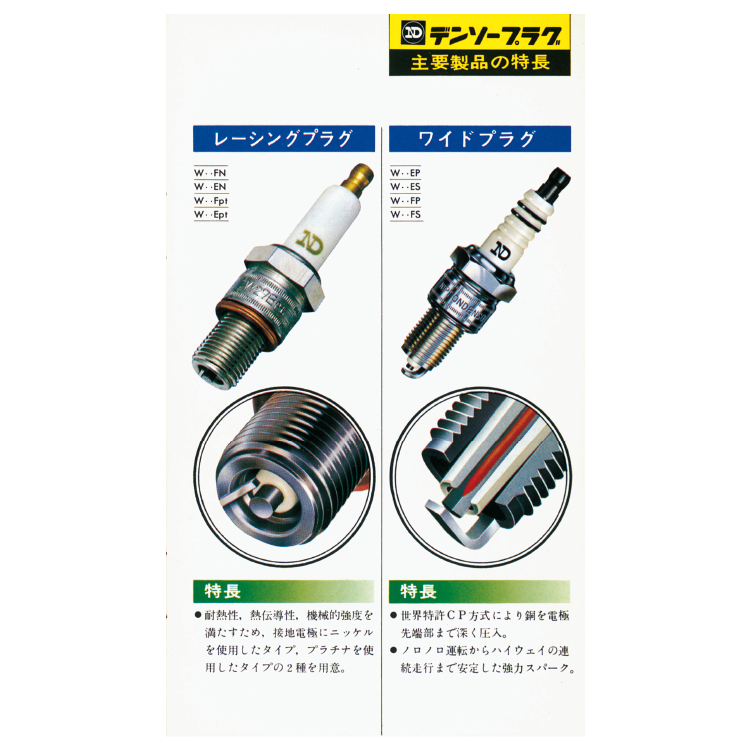
“Pocket Chart” (1972)
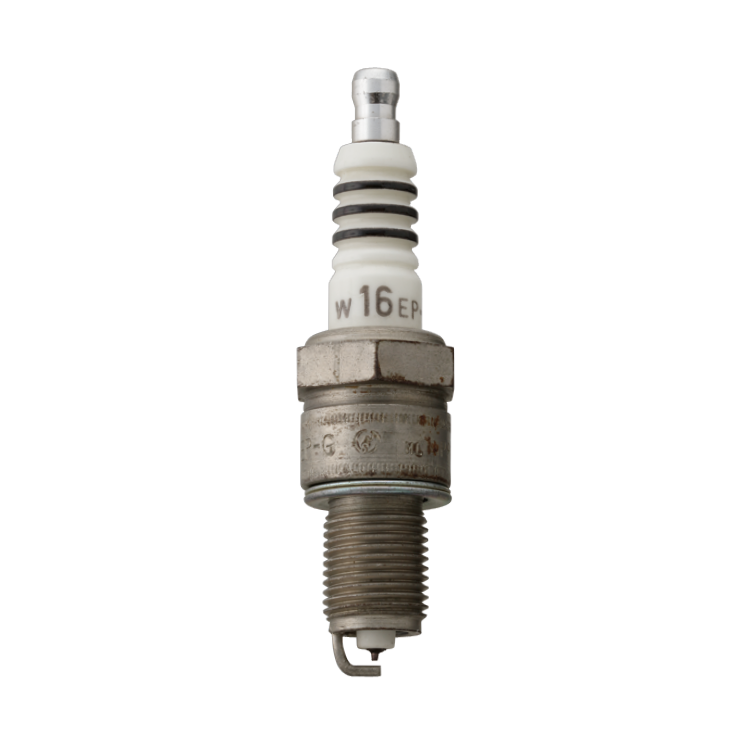
G plug
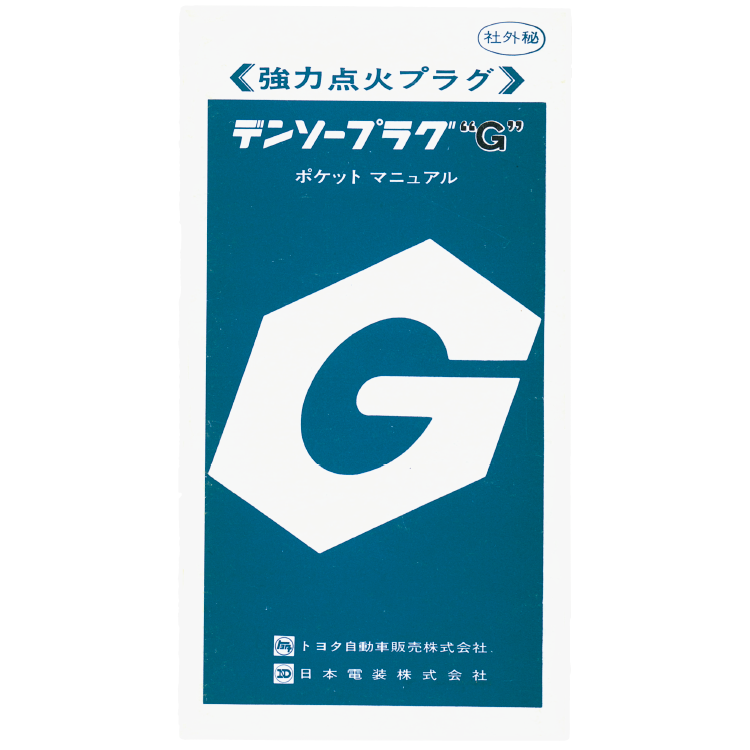
“DENSO Plug G” pocket manual (1972)
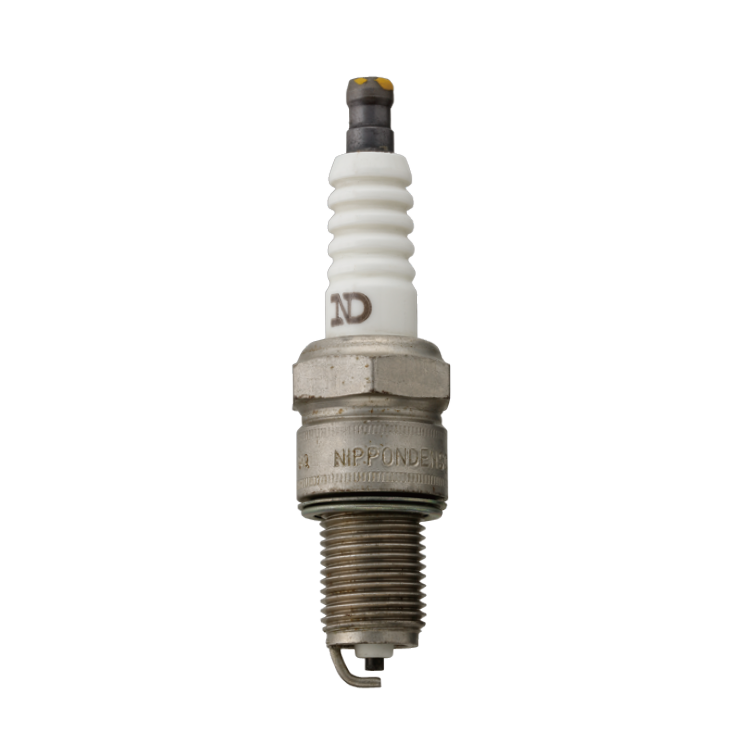
Resistor plug
1975
GU plug
3-electrode plug
Wide U Plug
1976
Double-electrode plug
1977
Semi-surface plug
1979
4-electrode plug
HISTORY
1975 – 1979
Company Background
A dramatic improvement in the performance and quality of spark plugs was required under emissions regulations starting in the 1970s.
To turn emissions green, a plug with a good ignitability to burn a lean mixture without having to dilute the fuel-air mixture is required.
Technology Development – Issues
To raise the ignitability of the plug, a variety of approaches from the perspective of the engine, ignition power source etc. is available.
It is necessary to prevent the energy of the flame kernel generated by electrical discharge from being absorbed by the center electrode and grounding electrode so as to reduce the flame extinguishing effect to allow the flame kernel to grow. To resolve the problem, methods such as using a wide gap and making the center electrode thinner etc. were already known.
However, it is also known that these methods have opposing disadvantages e.g. the sparking voltage rises, or the plug life is shortened and so on. Consequently, it was extremely difficult to find a solution, but the development team conducted a thorough study of the flame extinguishing effect and electrode shape to derive a conclusion.
Technology Development – Solutions
By making a U-shaped groove on the grounding electrode side, the same effect as a wide gap was realized. By studying the ignitability, heat resistance, producibility etc. and giving form to the conclusion, the world’s first U-groove plug was born.
Subsequently, improvements in the technology can also be seen in the plugs launched by other companies which have a cross-shaped or V-shaped groove on the center electrode side to achieve the same effect. Employing a U-shaped groove, the DENSO plug Wide U was awarded patents in 5 countries including the US, UK, France, Germany and Italy, becoming a globally patented plug both in name and reality.
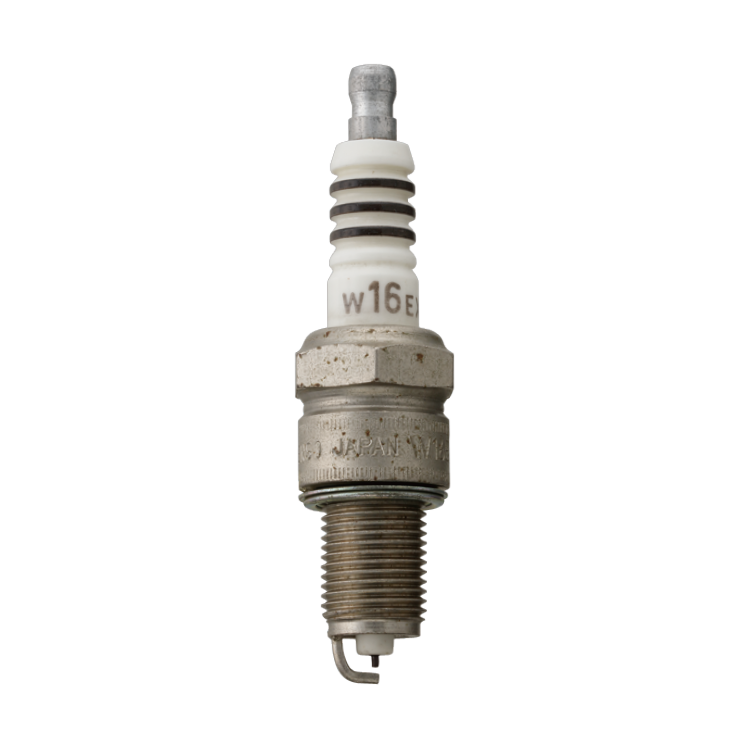
GU plug
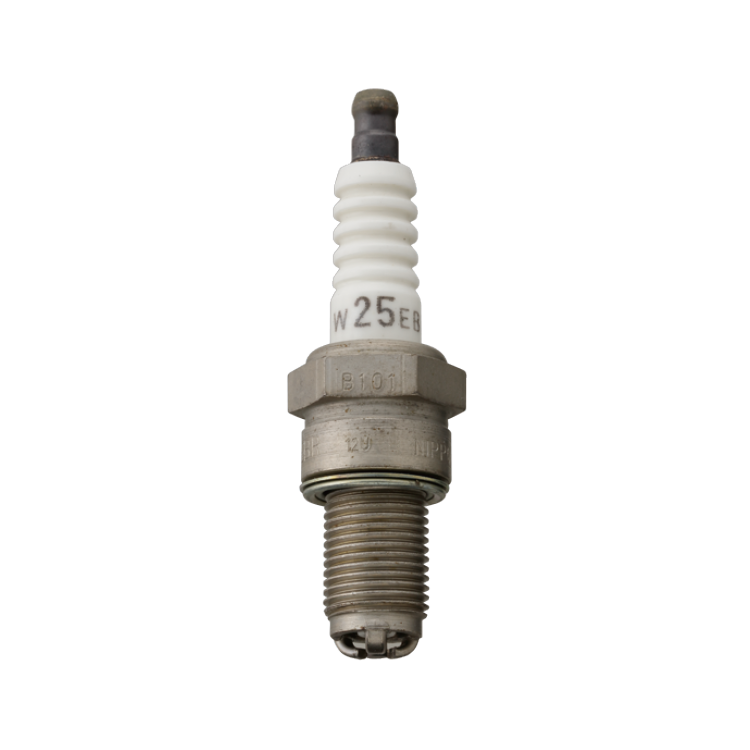
3-electrode plug
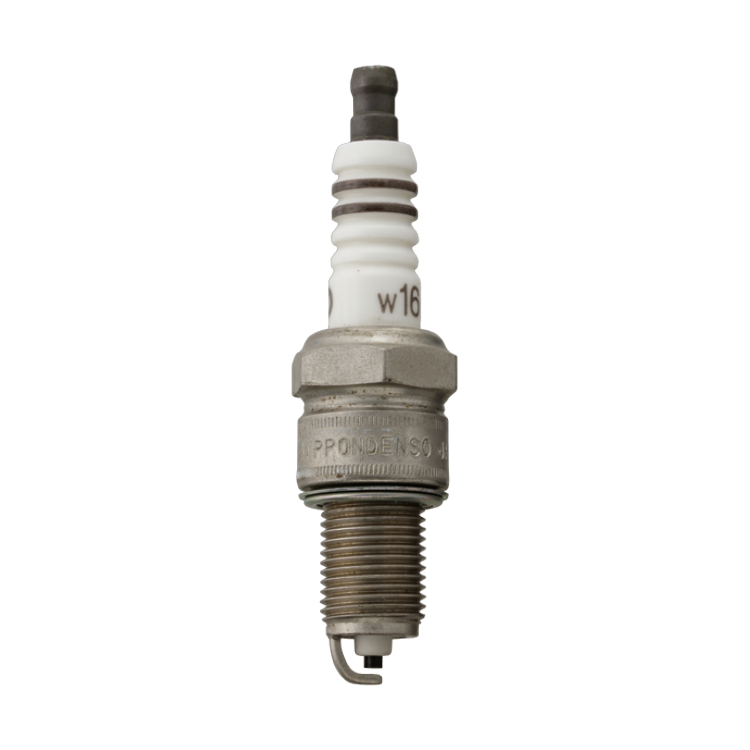
Wide U Plug
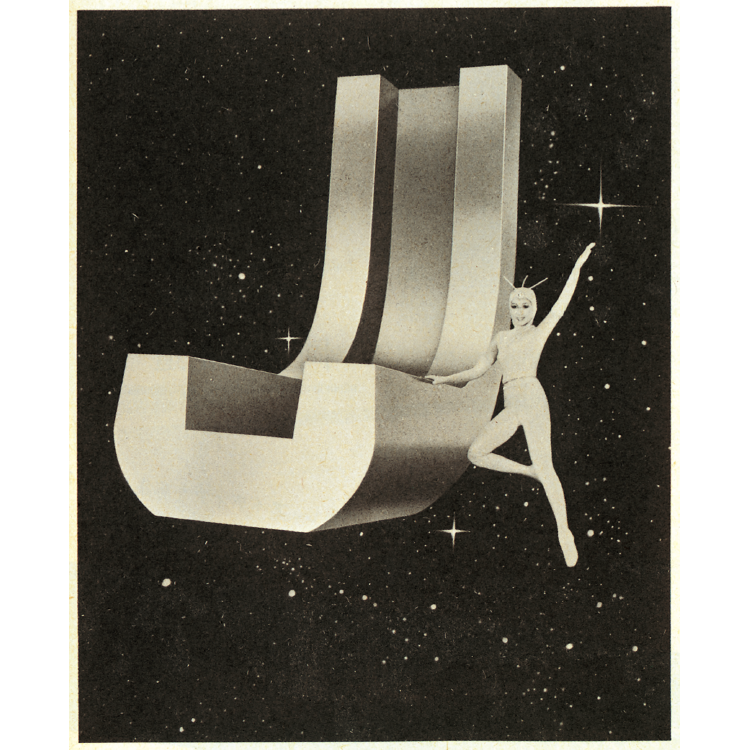
“Wide U Plug” record jacket
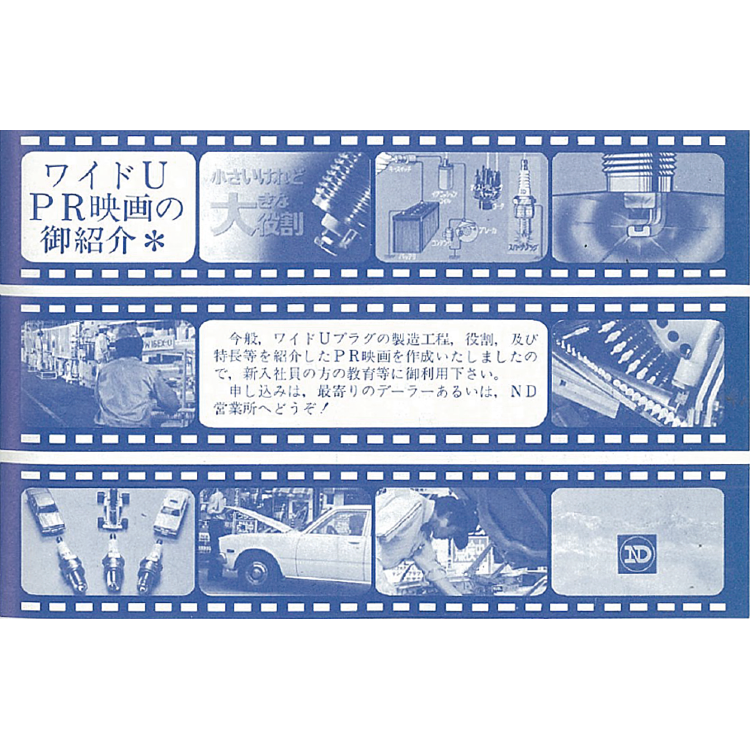
“Wide U Plug” TV CM
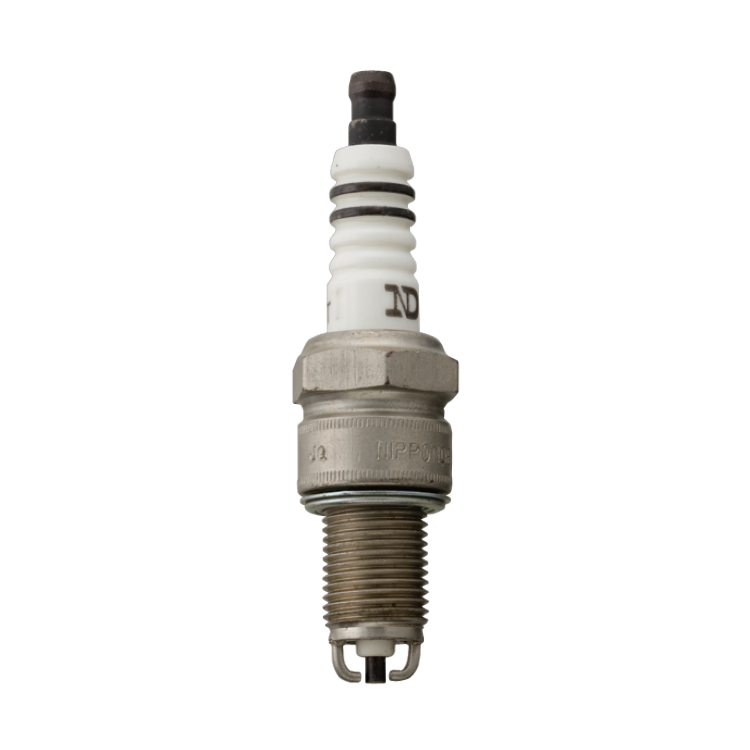
Double-electrode plug
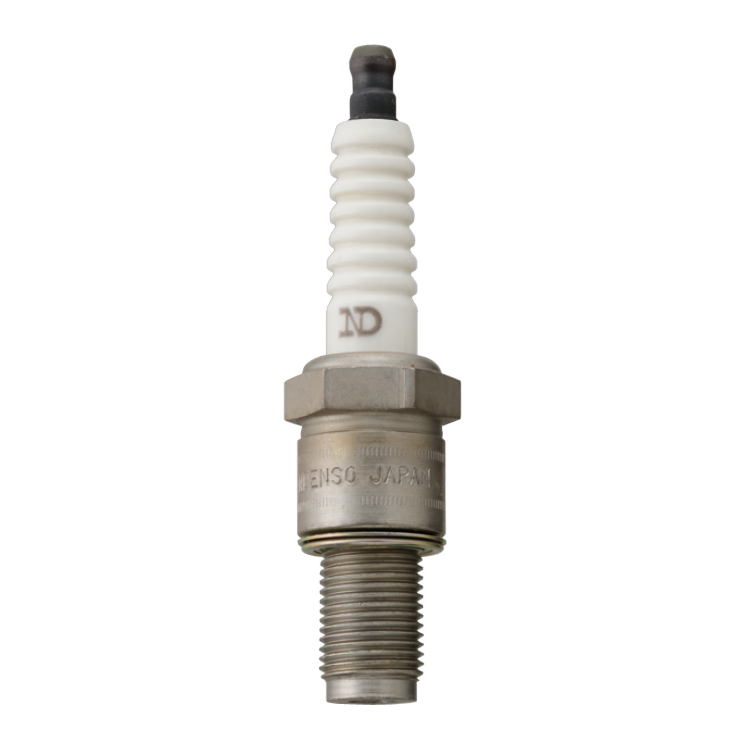
Semi-surface plug
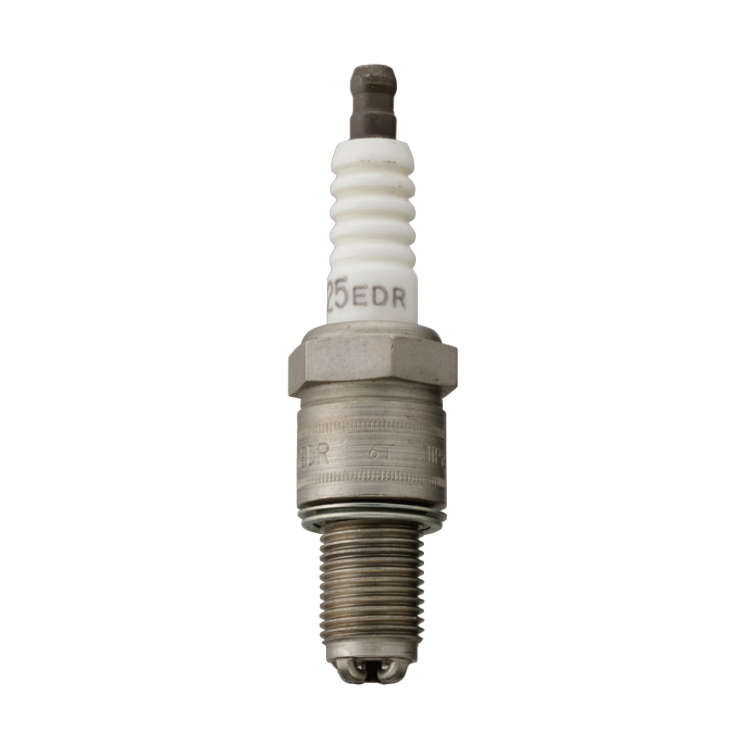
4-electrode plug
1981
Extended plug
1982
Small hex plug
Platinum plug
1983
ZU plug
1995
Double-electrode
Platinum plug
HISTORY
1980 – 1995
Company Background
At the beginning of the 1980s, combustion with an even leaner fuel-air mixture was required from the perspective of improving fuel efficiency and complying with stringent emissions regulations. Plugs were also required to tackle highly difficult challenges such as unprecedented improvements in the ignition performance and reducing the rise in the sparking voltage. Moreover, following improvements in engine performance, engine design became more complex, and plugs were also required to have a longer lifespan and be maintenance-free as it became difficult to install and remove the plugs.
Technology Development
To deal with such issues, the development staff focused their attention on platinum, a precious metal which has an excellent corrosion resistance and spark resistance, to make the center electrode thinner, and created a method to weld a thin platinum tip on only the electrode discharge section so as to keep the cost low.
However, it did not mean that the technical problems were resolved with this. Due to the difference in the coefficient of expansion between platinum and the electrode base material, a problem occurred due to the platinum tip peeling off. Therefore, we finally succeeded in commercializing the product by controlling the changes in the platinum thickness after welding and the thickness of the alloy layer at the bonding boundary in micron units, in addition to strictly controlling the material of the platinum tip and the power conditions of the resistance welding. We were then able to file a patent for it too. In this way, a platinum plug employing a platinum tip only in the electrical discharge section was launched in Aug 1982.
Development After Launch
This platinum plug has a durability of 100,000 km and was mainly installed in Toyota cars for the US market initially. Subsequently, it was employed in other cars one after another such as taxis which have a high mileage, one-box cars for which it is difficult to replace the plugs due to the engine mounting position, luxury cars which need to be maintenance-free and so on.
Technology Development
In 1983, the ZU plug was developed for users who prefer high performance plugs. Initially, this newly developed ZU plug was used experimentally by race users etc. for road races, motocross and dirt races in the US, but it was then launched officially as a high grade type of general plug.
This ZU plug employed platinum in the center electrode to realize a center electrode with the world’s smallest diameter (0.7 mm) at that time. Furthermore, we succeeded in improving the sparking performance and ignition performance by employing a taper cut at the tip of the grounding electrode. By using a center electrode with a fine diameter of 0.7 mm, it is possible to create sparks at a low voltage, allowing a good starting characteristic and efficient combustion to be obtained.
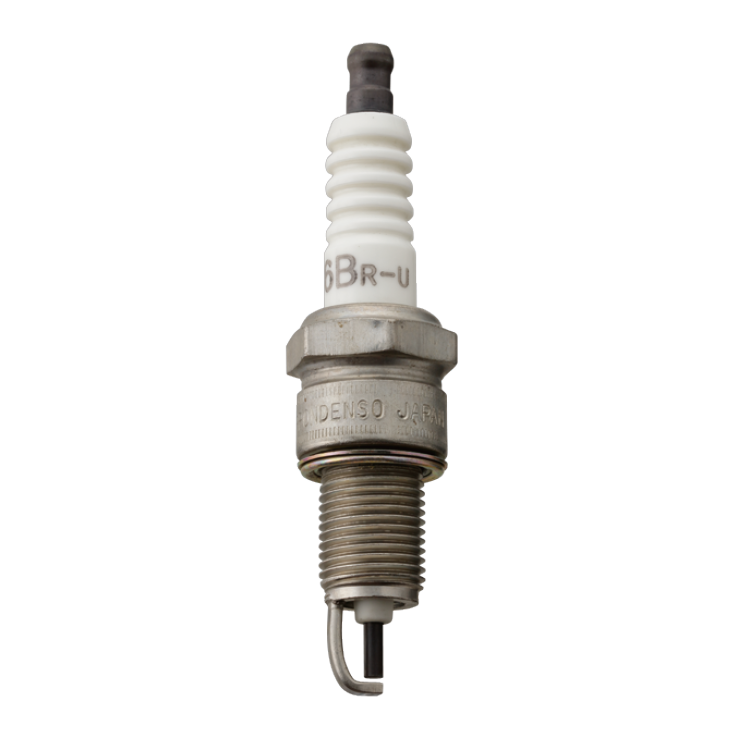
Extended plug
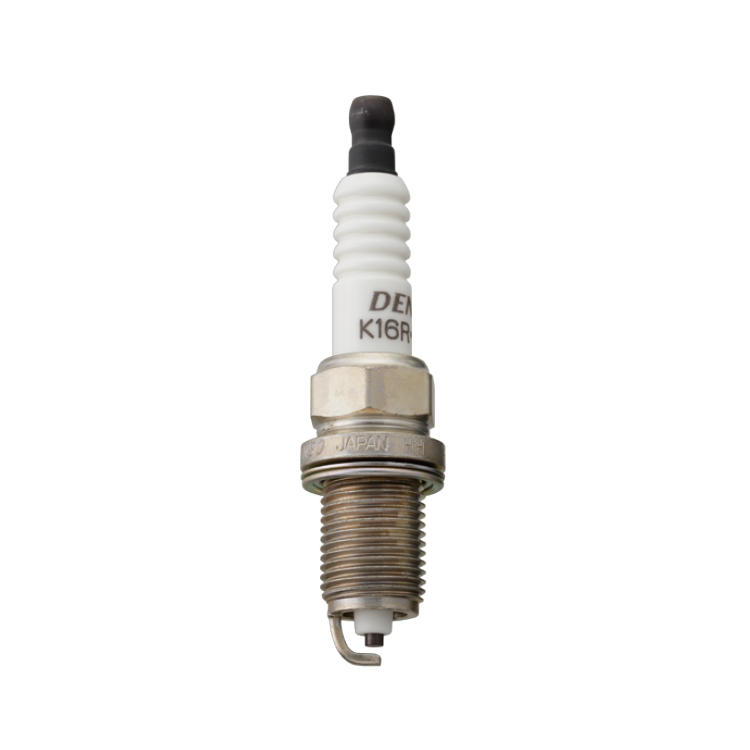
Small hex plug
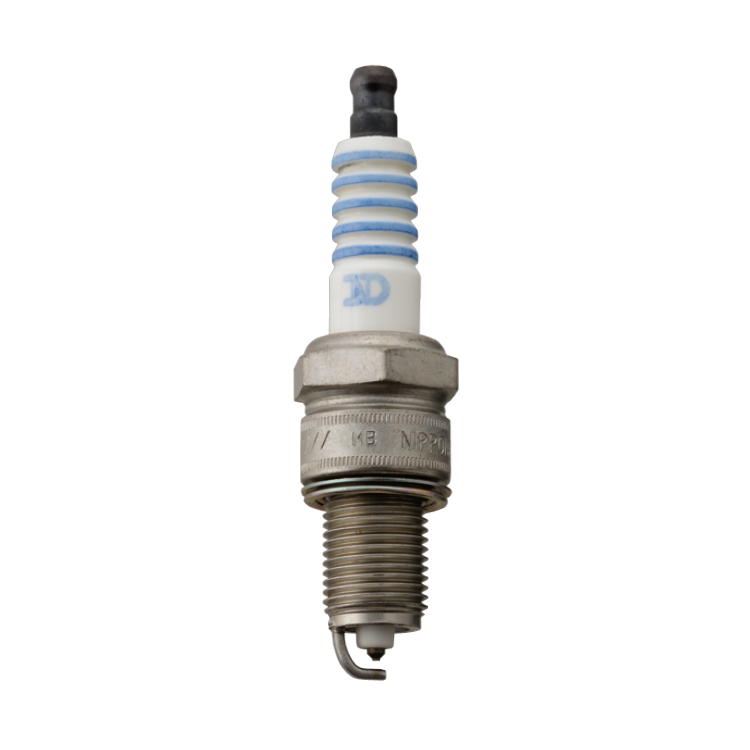
Platinum plug
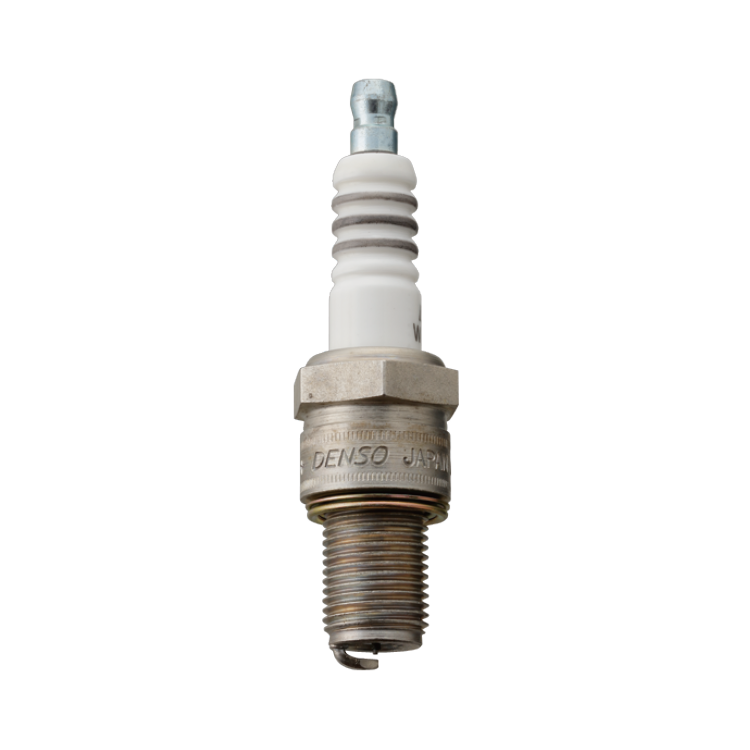
ZU plug
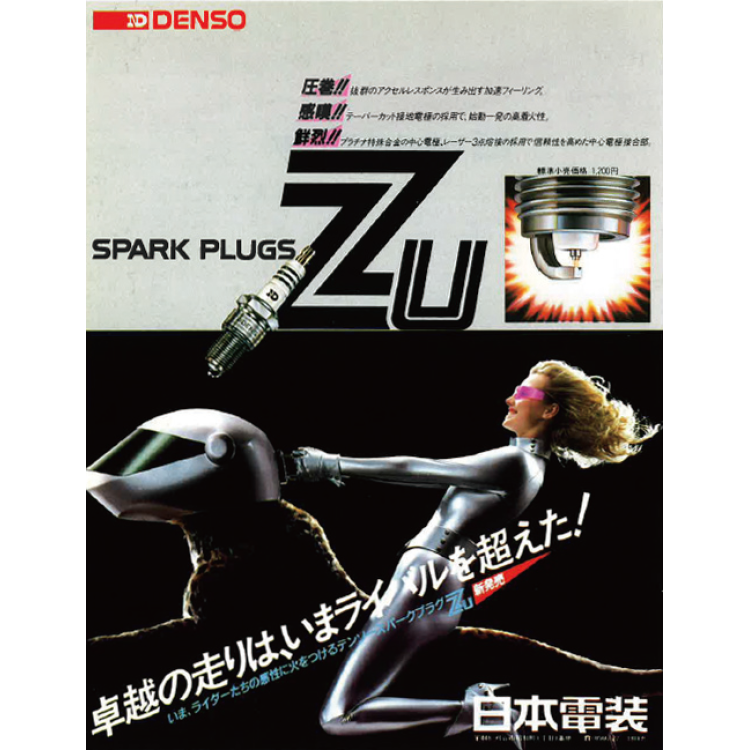
“ZU Plug” leaflet
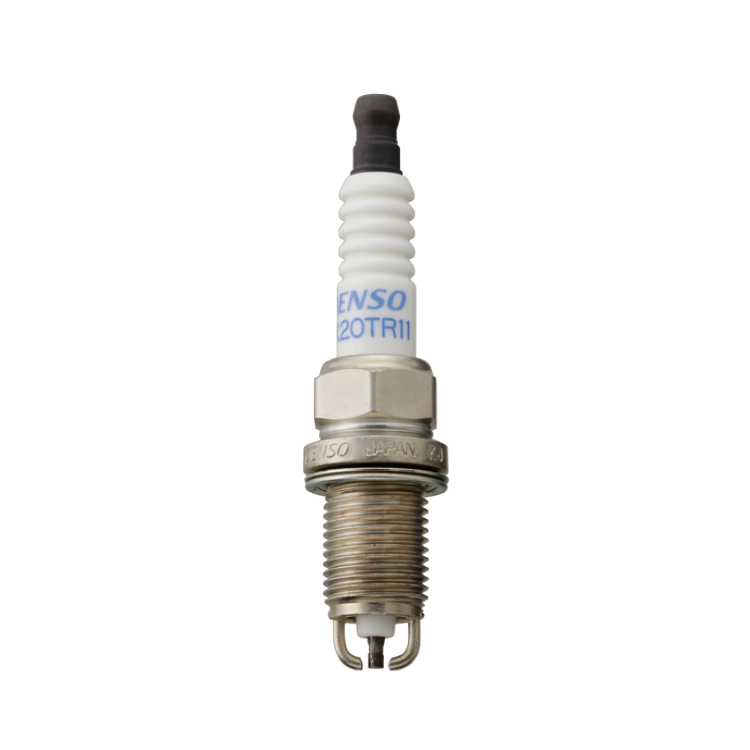
Double-electrode Platinum plug
1997
Iridium plug
1998
IRIDIUM POWER
2003
Double needle
Iridium plug2008
TT plug
2018
Total production of
6 billion plugs
achieved
HISTORY
1996 – 2018
Technology Development
In 1997, the company developed a new plug using a precious metal as a base to replace the platinum plug. This is the iridium plug with an ultra-thin electrode which made it possible to extend its life by using an iridium alloy in the center electrode.
The iridium plug dramatically improves the wear resistance compared to previous platinum plugs, allowing the electrode to be made even thinner and further improving the ignitability and electrical discharge property compared to before.
Besides achieving an astonishing durability of 200,000 km with its focus on the lifespan, the iridium plug also succeeded in stabilizing the combustion.
In 1998, based on the technology developed, we created a new generation of high-performance plugs employing an iridium alloy with a diameter of 0.4 mm.
Named as [IRIDIUM POWER], this plug succeeded in lowering the sparking voltage and improving the ignition performance by employing a grounding electrode which combines our proprietary U-groove and taper cut, and an ultra-thin center electrode with the world’s smallest diameter of 0.4 mm, allowing a reliable combustion to be obtained in all operating ranges.
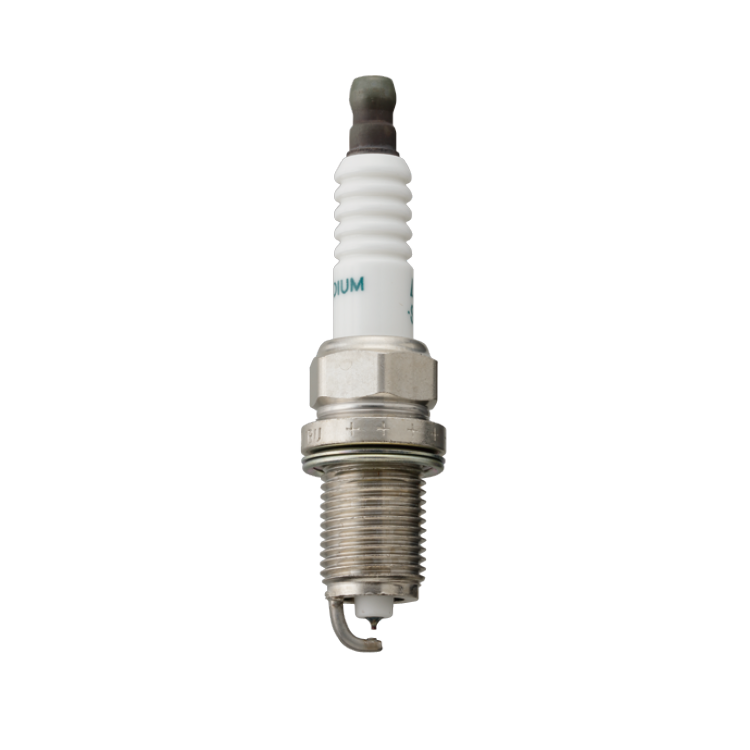
Iridium plug
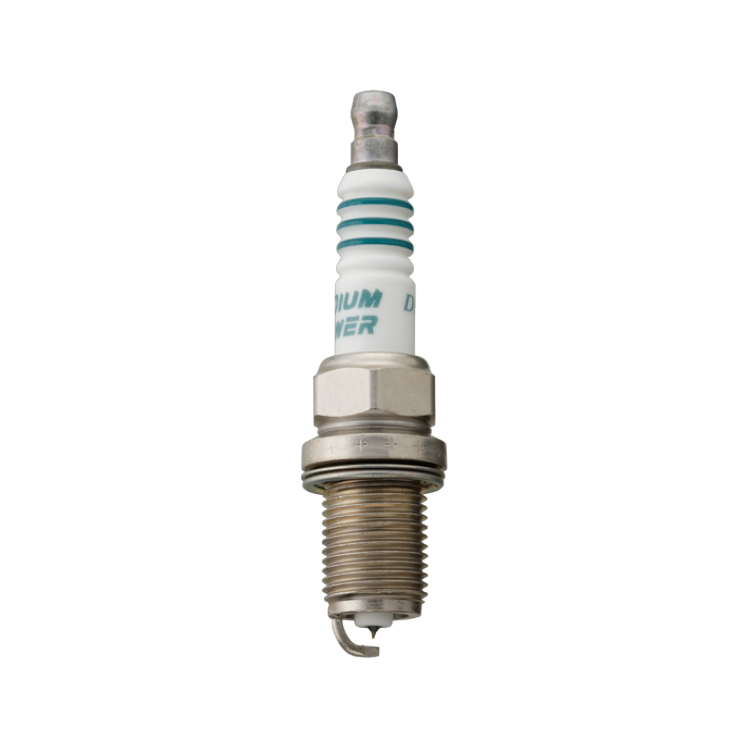
IRIDIUM POWER
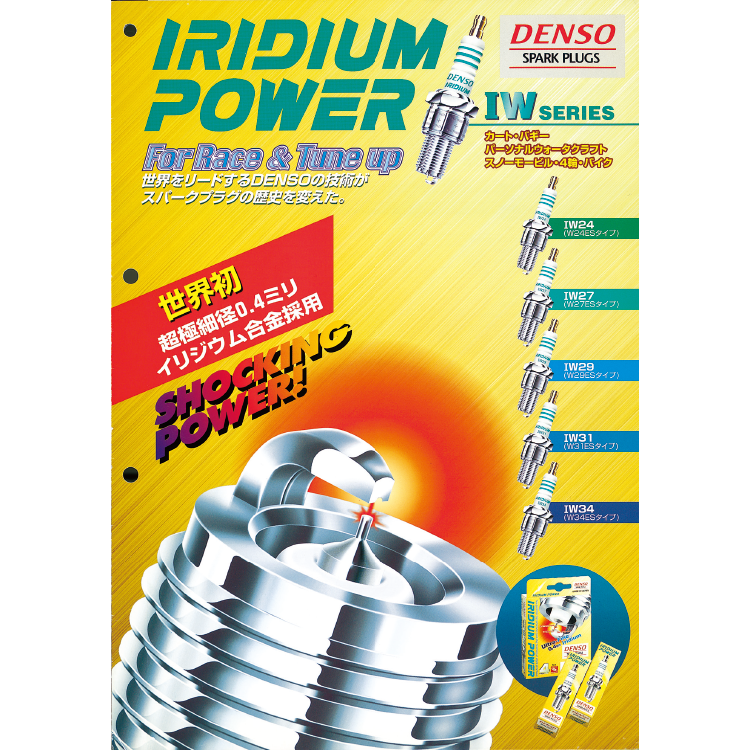
“IRIDIUM POWER” pamphlet
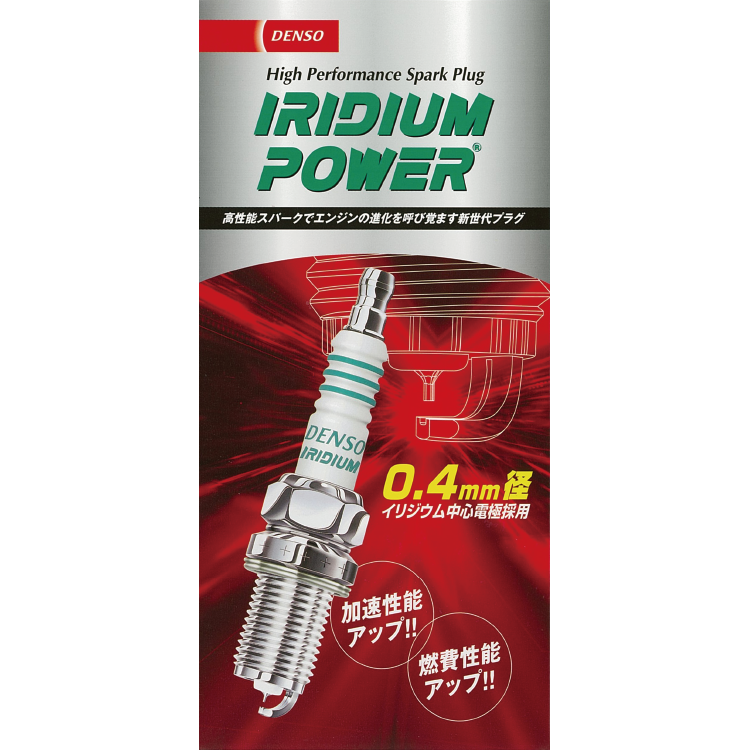
“IRIDIUM POWER” POP
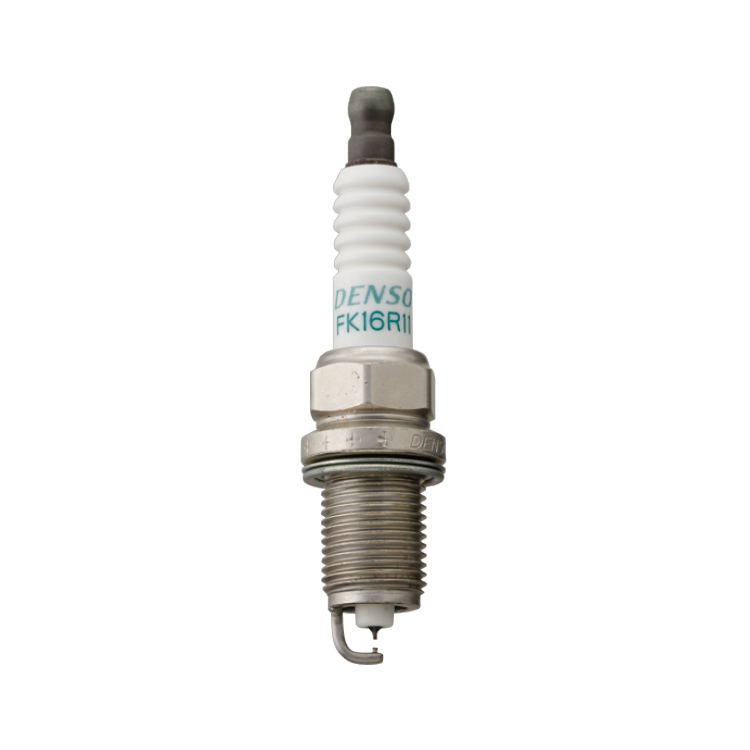
Double needle Iridium plug
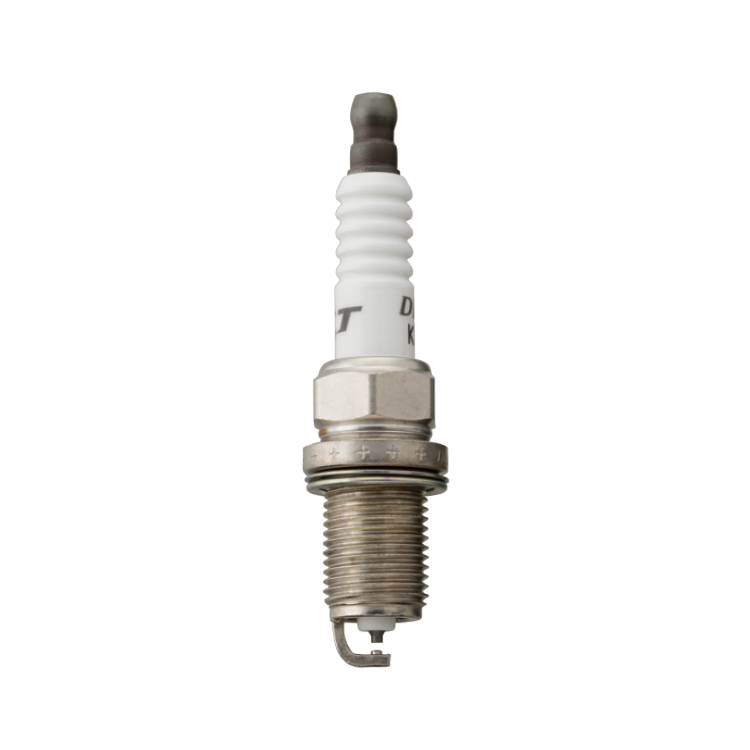
TT plug